Rechercher
Derniers sujets
» Visu Ariège Septembre 2025par chris 36 Aujourd'hui à 11:20
» Malus pour voitures neuves et d'occasion, le gouvernement veut tout augmenter
par chris 36 Aujourd'hui à 11:19
» Fin de ma période Goldwing
par Claude 38 Aujourd'hui à 9:44
» Vidéos à la suite....
par g2loq Aujourd'hui à 9:25
» Une image marrante ou insolite par jour...en forme toujours
par g2loq Aujourd'hui à 8:54
» elle est bonne ! (vos blagues du jour ici)
par easy rider Aujourd'hui à 7:31
» Un belge en plus en Goldwing (Axelfoley)
par charpentier09 Hier à 22:55
» Balade des Papas Noël motards Toulousains con
par chris5 Hier à 19:34
» Château Lavardens et ses expositions dont des santons
par chris5 Hier à 18:33
» Citations
par g2loq Hier à 17:18
» Joyeux anniversaire aujourd'hui à ...
par Etche Hier à 11:53
» Météo
par DenisFont85 Hier à 6:13
» Rencontres toulousaines
par chris5 Mar 19 Nov 2024 - 20:48
» origine de votre pseudo
par Axelfoley Mar 19 Nov 2024 - 18:43
» Malus bruit sur les motos en 2025
par boris-jc Lun 18 Nov 2024 - 17:21
» Que se passe t'il au jardin?
par eddy tionspéciale Lun 18 Nov 2024 - 16:31
» Le V6 PRV fête ses 50 ans, et il vaut mieux que sa réputation !
par g2loq Lun 18 Nov 2024 - 9:33
» historique modèles goldwing et leur immatriculation (VIN)
par g2loq Sam 16 Nov 2024 - 22:29
» Fanion FGI - commande
par Buxenus Sam 16 Nov 2024 - 16:41
» Besoin de conseils de briscard.e.x
par didier Sam 16 Nov 2024 - 15:03
Qui est en ligne ?
Il y a en tout 621 utilisateurs en ligne :: 19 Enregistrés, 0 Invisible et 602 Invités :: 3 Moteurs de rechercheBLACKBIRD38, bob25, chris 36, chris33, chris5, DOUDOU94, El_TiTeP, Etche, Filip78, Flip, g2loq, Gekko, GuismoGold, jacquesolivier, jcdu47, Kebra, phiphi 60, Pépé69, Wild-Weasel
Le record du nombre d'utilisateurs en ligne est de 1170 le Mar 5 Déc 2023 - 20:42
Connexion
Les secrets de fabrication des casques Arai
Page 1 sur 1
Les secrets de fabrication des casques Arai

par Damien Bertrand | 03.04.2024
Les secrets de fabrication des casques moto
Visite des sites de production d'Arai au Japon
5 sites, 350 employés et une production presque artisanale
Arai… incontournable, référence mondiale, la fabrique nippone de casques motos nous ouvre donc ses portes, au Japon. 5 sites regroupant 350 employés nous accueillent, à commencer par celui d’Omiya, lieux historique et originel de la firme où notre visite commence.
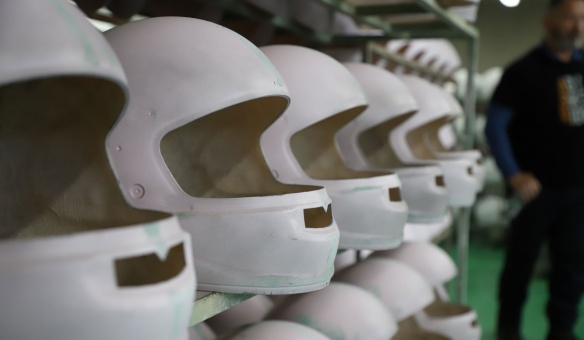
Les secrets de fabrication des casques Arai
Omiya - le site historique
C’est en effet là que le fondateur de la société, Hirotake Arai, fabriquait des chapeaux depuis 1926.
Également motard, il développe ensuite ses premiers casques, notamment pour protéger les ouvriers sur les chantiers. Mais après la Seconde Guerre mondiale, il n’y avait pas de machine pour cet usage et pour ce faire, Hirotake récupère les surplus de casques de l’armée américaine. Cependant, il commence rapidement à concevoir des coques en fibre de verre, procédé totalement novateur à l’époque.
Son intention n’était pas de démarrer une autre activité commerciale, mais de créer des casques capables de protéger aussi ses collègues motards. La protection, cette notion essentielle toujours présente aujourd’hui au sein de la société Arai.

C'est à Mitchio Arai, fils du fondateur, que l'on doit l'essor international de la marque
C’est son fils Mitchio Arai, ou « Mitch », qui va véritablement développer la société, tant technologiquement qu’à l’exportation internationale. Son bon niveau d’anglais, acquis aux États-Unis, lui permet d’assurer la communication de son entreprise. À l’époque, la marque Bell y est numéro un au nouveau monde. Mais Mitch constate que, quelle que soit leur origine, les casques ne se démarquent pas vraiment en termes de qualité. Il décide alors, au début des années 70, de dominer le marché sur un point fondamental : la protection.
Chez Arai, au fur et à mesure des recherches, un standard va s’imposer comme base : le R75. Cette notion définit un rayon de coque incurvé convexe et continu de 75 mm. Plus ronde et lisse, la coque est ainsi mieux à même de ricocher sur les obstacles et glissent plus facilement sur des surfaces inégales. Enfin, elle minimise l’énergie d’impact envoyée directement dans le casque que le calotin intérieur doit absorber.

La rondeur de la coque, la fameuse R75, est au coeur de la sécurité des casques Arai
Au sein de l’usine d’Omiya se trouve toujours l’atelier de réalisation des moules, déjà présent dès 1965. Désormais, leur fabrication est réalisée par fraiseuses 3d. Il faut 8 heures pour le finaliser à partir d’un bloc d'acier. Arai défini 3 moules par tailles de coques et réalise généralement 4 exemplaires pour chaque taille.
Shinto factory - création des coques
Ici, 900 coques par jour (soit environ 270.000 par an) sont produites. Tout commence par la formation du « bird nest » – nid d’oiseau, structure qui va former la base du casque. Des « Superfibre » brutes de 9 microns, à peine visible sont tissées en cordon. Leur densité très importante engendre une très grande résistance. Cet assemblage est ensuite projeté en morceaux de 5 centimètres sur une forme sous laquelle est placé un système d'aspiration. Cela crée ainsi cette fameuse demi-sphère de base. Elle pèse alors 80 grammes, pour une épaisseur de 3 mm. Ce processus est contrôlé à tout moment en densité, nombre de fibres... Etc. Une correction rapide est apportée si un problème est détecté. Ce sont de toutes nouvelles machines, à 5 millions d’euros par pièce.

Tout commence par la création d'un chausson léger en fibres de verre, le bird nest
Dans un bâtiment annexe est concentrée la préparation des différentes fibres de renforts, notamment le panneau de « Superfibre » au niveau de la future découpe de l’écran.
Plusieurs postes assemblent les différentes couches de fibres et « d'ARmat » nécessaires à la fabrication en plus du nid. Type de casque et tailles déterminent les dimensions. Chaque feuille est découpée et placée en ordre sur la balance. Pour le principal renfort, six différents éléments et un maillage carbone sont assemblés.
Egalement, nous avons accès au module de tissage des bandes de « Superfibres » pour les renforts arrière et bords supérieurs de la découpe d'écran. A l’origine, c’était une machine pour tisser les ceintures de sécurité. 32 fines cordelettes sont assemblées, jouxtées de deux fils de maintien latéraux.

L'atelier de tissage des bandes de 'Superfibres' qui servent à rigidifier la calotte
Vient enfin la fabrication de la coque au sein du moule. Chaque opérateur sait exactement comment procéder suivant une fiche détaillant le type, la taille et même la destination du casque !
La matrice est chauffée à 100 degrés et les étapes successives demandent une année de formation pour pouvoir exercer. Une preuve de la nécessité d’une excellente maitrise. En effet, la plupart du temps ces manipulations sont réalisées sans gant pour assurer un ressenti optimal du positionnement des différents composants. Un premier ensemble de plusieurs couches formant la coque est placé dans le moule. Est ensuite ajouté un renforcement frontal, puis un liner pour la partie supérieure du dégagement oculaire. Vient ensuite la mentonnière, puis une fibre très résistante « d’ARmat » placé sur les côtés et enfin du « Zylon » (sorte de kevlar) sur le sommet interne. Un nouveau « nid » est inséré pour prendre un sandwich le tout. Une résine est ensuite coulée et le couvercle muni d’un ballon gonflé sous pression vient presser l’ensemble pendant 10 min. Quand le moule s’ouvre, la coque brute est alors extraite pour être numérotée et une première fois pesée. Procédure très importante, cette vérification du poids, permet déjà de vérifier que tous les composants ont été placés. Elle est plusieurs fois répétée durant la fabrication.

Les coques brutes telles qu'elles sortent de la Shinto Factory
La coque passe ensuite dans un autre four à 100 degrés, très sec, pour renforcer la résine. Et à nouveau, passage sur la balance.
Les coques passent ensuite à la découpe au laser. Cette automatisation a nécessité un calibrage très précis du module de découpe. A la suite, un premier contrôle de l'épaisseur est réalisé. Les rares défauts ont la possibilité d’être corrigés par rajout de patchs de super fibres.
Amanuma : centre de contrôle secondaire des coques.
10 000 coques sont ici stockées ! Et chacune est à nouveau testée par deux personnes. Un numéro en vert dans la coque signait la première inspection visuelle. La vérification que tous les composants sont bien placés. Ici est désormais réalisé un contrôle de l'épaisseur de chaque coque et des zones spécifiques aux normes. Enfin le poids est, à nouveau, mesuré pour s'assurer que le casque possède bien tous les composants nécessaires. Si tout est conforme, un nouveau numéro, en rouge, est apposé.
Il n’y a quasiment aucune pièce refusée.

À Amanuma, chaque coque est testée et contrôlée deux fois
Minamidai - Usine Peinture
Les coques arrivent brutes. Elles reçoivent une argile dispersée à l'éponge pour ne combler que les micro-défauts. Ensuite est déposée au pistolet une couche de primaire. Un nouveau passage balance permet de vérifier la bonne quantité de produit dispersée. S'en suit un contrôle de surface et corrections des défauts puis ponçage à l'eau. Ces opérations sont répétées deux fois pour les retouches et trois pour le ponçage. Une étape qui demande cinq jours pour que tout soit parfaitement surfacé.

Les coques sont peintes avec une sous-couche avant un nouveau contrôle
Viennent ensuite les peintures à proprement dites. Une fois les teintes appliquées, les décorations sont réalisées dans autre niveau. Une zone d'acclimatation est aménagée entre les deux pour ne pas abîmer les surfaces. Des repères sont définis pour apposer précisément les transferts par eau. Ensuite, les casques sont passés au vernis de protection multicouche avant une dernière étape.

Comme chaque étape de production, l'application des décorations se fait à la main
Katayanagi - Usine Assemblage
Le travail commence ici par une vérification des surfaces et un polissage doux des vernis avec retouches éventuelles. C’est ensuite le perçage des différents évents de ventilation puis l’assemblage des joints et pose des commandes d’aération.

En toute fin de processus, les ventilations et sont percées dans la coque
L’opération qui vient ensuite demande une
certaine force et habileté. En effet, la mise en place du calotin déjà équipé de l'habillage léger en mesh n’est pas une évidence aux profanes. Rappelons que la fabrication du calotin en EPS multi-densités d’une seule pièce est un secret professionnel.
Suit le rivetage de la jugulaire, le montage des divers coussins de mousse puis des derniers éléments de ventilation et des platines de l'écran.

L'assemblage final est réalisé à Katayanagi
Enfin, c’est la mise en place des autocollants extérieurs siglés Arai (frontal, arrière) et informations intérieures.
Un ultime polissage et c’est la mise en sac puis carton.
Voilà votre casque prêt ! A l’issue de ces nombreuses étapes, vous pouvez ainsi vous rendre compte de la qualité artisano-industrielle mise en œuvre pour réaliser chaque modèle signé Arai. Une cinquantaine d’opérateurs ont eu votre futur casque en main et pris un soin hors norme pour le vérifier, le finaliser. Toute la production de la firme est faite au Japon afin de conserver les emplois et assurer une qualité exemplaire.

Après être passé entre les mains d'une cinquantaine de personnes, le casque Arai est prêt à être vendu
Quand vous passerez pour la première fois votre casque fois sur votre précieuse tête, songez qu’Arai à mis tout son savoir-faire pour l’assurer de sa qualité première : sa protection.
Plus d'infos sur Arai
Site : www.araihelmet.eu
Damien Bertrand

Ne dites pas à ma mère que je suis co-admin chez FGI


g2loq- Co-administrateur
- Messages : 22938
Date d'inscription : 29/04/2013
Age : 70

» Les secrets de la fabrication du pneu - partie I (+vidéo)
» Casque ARAI assorti
» Casque Arai goldwing
» ARAI TOUR-X4 - Voyageur de luxe
» Interview Dai Arai, le "père" de la transmission DCT Honda
» Casque ARAI assorti
» Casque Arai goldwing
» ARAI TOUR-X4 - Voyageur de luxe
» Interview Dai Arai, le "père" de la transmission DCT Honda
Page 1 sur 1
Permission de ce forum:
Vous ne pouvez pas répondre aux sujets dans ce forum